From Design to Finish: The Full Light Weight Aluminum Casting Refine Demystified
In the realm of production, the procedure of aluminum casting stands as a crucial method that has actually fueled industries for decades. Each action in this intricate process, from the preliminary style phase to the last complements, plays a critical role fit the result of the product. What genuinely exists underneath the surface of this procedure continues to be a secret to lots of. By unwinding the intricacies and losing light on the subtleties involved in each stage, a deeper understanding of the art and science behind aluminum spreading emerges. about aluminum casting. Stay tuned as we dissect the full light weight aluminum casting process, uncovering the ins and outs that transform resources into polished products.
Designing the Casting Mold
When initiating the aluminum casting process, careful attention to creating the casting mold is critical for making certain the end product's integrity and high quality. The spreading mold serves as the structure for the entire spreading procedure, dictating the form, measurements, and surface coating of the eventual light weight aluminum part.
To make an efficient casting mold and mildew, designers have to think about various aspects such as the intricacy of the component, the type of light weight aluminum alloy being made use of, and the desired buildings of the end product. about aluminum casting. Computer-aided design (CAD) software program is often utilized to develop comprehensive schematics of the mold, permitting specific modification and optimization
Additionally, the style of the casting mold and mildew straight influences the efficiency and cost-effectiveness of the casting procedure. A properly designed mold decreases product waste, reduces the need for extensive post-casting machining, and improves general manufacturing rate.
Melting and Pouring Aluminum
With the design of the spreading mold and mildew settled, the next critical action in the aluminum casting procedure is the melting and putting of the light weight aluminum alloy. The process begins with filling the light weight aluminum alloy right into a furnace where it is warmed to its melting factor, generally around 660 ° C(1220 ° F) for aluminum. Crucible furnaces, induction heating systems, or gas-fired reverberatory heaters are frequently utilized for melting aluminum. As soon as the light weight aluminum is liquified, it is essential to keep the temperature level within a details variety to ensure the high quality of the spreadings.
After the aluminum reaches the preferred consistency, it is time for putting. The molten aluminum is meticulously transferred from the furnace to the spreading mold. This step calls for precision and control to stay clear of problems in the end product. The putting process must be executed swiftly to avoid early solidification and make certain the aluminum loads the mold and mildew completely. Correct putting methods contribute dramatically to the general quality of the last light weight aluminum casting.
Strengthening and Cooling Refine
Upon completion of the putting process, the liquified light weight aluminum transitions into the cooling and strengthening phase, an important stage in the light weight aluminum spreading procedure that directly influences the final product's stability and qualities. As the light weight aluminum starts to cool down, its molecules prepare themselves into a strong kind, gradually taking on the form of the mold. The rate at which the light weight aluminum cools down is critical, as it influences the product's microstructure and mechanical homes. Rapid air conditioning can look at this now lead to a finer grain structure, boosting the product's stamina, while slower air conditioning may result in larger grain sizes, affecting the end product's ductility.
During this phase, it is important to regulate the cooling process thoroughly to prevent look at here flaws such as porosity, shrinking, or interior tensions. Different air conditioning approaches, such as air cooling, water quenching, or controlled cooling chambers, can be used based on the specific demands of the casting (about aluminum casting). By controling the solidification and checking and cooling down procedure, manufacturers can guarantee the production of top quality aluminum castings with the wanted mechanical and metallurgical residential or commercial properties
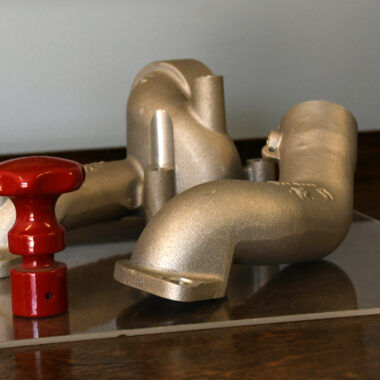
Getting Rid Of the Final Casting
As soon as the light weight aluminum casting has completely solidified and cooled in the mold, the following action in the procedure includes carefully eliminating the last casting. This step is essential to make sure that the light weight aluminum component is successfully drawn out without any damages or flaws.
To remove the casting, the mold and mildew is opened, and the spreading is removed utilizing different methods relying on the complexity of the mold and the part layout. For easier forms, the casting can frequently be easily removed by hand or with straightforward tools. Nevertheless, for more intricate designs, extra equipment such as ejector pins, air blasts, or hydraulic systems might be called for to assist in the removal process without creating any harm to the spreading.
After the casting is effectively removed from the mold, any kind of excess product such as entrances, joggers, or risers that were utilized during the spreading procedure are cut off. This action helps in achieving the last desired shape of the light weight aluminum component prior to it undergoes any type of additional completing procedures.
Finishing and Quality Assessment
The last in the light weight aluminum spreading procedure involves careful finishing strategies and extensive top quality examination procedures to make sure the honesty and precision of the cast aluminum components. Completing strategies such as grinding, fining sand, and shot blasting are utilized to eliminate any excess material, smooth harsh surface areas, and improve the visual appeal of the end product. These processes not just boost the look however additionally make certain that the parts fulfill the specified dimensional resistances and surface area finish needs.

Final Thought
In verdict, the aluminum casting procedure includes making the mold and mildew, melting and putting light weight aluminum, strengthening and cooling down the casting, removing the end product, and completed with a top quality examination. Each action is essential in making sure the last product meets the desired requirements. By understanding the entire procedure, makers can create high-quality light weight aluminum spreadings successfully and properly.
Remain tuned as we dissect the full light weight aluminum casting procedure, revealing the intricacies that transform raw products into polished products.
With the design of the spreading mold and mildew completed, the next important action in the aluminum casting procedure is the melting and putting of the light weight aluminum alloy.Upon completion of the putting procedure, the liquified aluminum changes right into the solidifying and cooling stage, a vital phase in the light weight aluminum spreading process that directly affects the last product's stability and characteristics.The final stage in the aluminum casting process involves thorough finishing techniques and strenuous top quality examination protocols to make sure the honesty and precision of the cast light weight aluminum parts.In final thought, the light weight aluminum casting process entails making the mold, melting and pouring light weight aluminum, strengthening and cooling down the casting, removing the final product, and finishing with a quality assessment.